LED moulding
LED casting or LED moulding is suitable for almost any application. It concerns a technique in the LED technical field that is used to strengthen and waterproof LED installations. By LED moulding with a casting resin or polyurethane, a transparent waterproof layer is created over the LED application. This layer offers protection to the housing of the LED and therefore the LED application can be used in applications and in places for which it was previously not suitable.
LED casting according to application
When pouring in, the use of the LED application and the requirements set for the order are always taken into account. To meet such requirements, LuxaLight has a department that focuses entirely on LED moulding. All applications are poured into a conditioned space to ensure consistent quality. The casting itself is done with different casting resins. The application and the requirements set determine which casting resin should be used. The options for casting are therefore very diverse and depend on the order.
Reinforces positive qualities
Positive properties are enhanced by pouring in the application. Positive properties of embedded LED applications are, for example;
- Protection against extreme influences such as chemicals and weather conditions
- Shock and vibration resistance, extends component and solder life.
- Very strong and durable up to an IK value of 10 (vandal resistant)
- UV-resistant so does not discolour / yellow
- Better mechanically loadable (extremely suitable for LED in pavements and floors)
- Completely waterproof (up to class IP68) while preserving the heat dissipation, allowing large powers in LED installations
- Warranty from 5 to 10 years
Level of transparency
The embedded LED applications are available in different levels of transparency, depending entirely on the application. By implementing several layers of polyurethane or silicone, it is possible to obtain a different degree of transparency, for example completely clear (hotspots visible), semi-diffuse (partially visible) diffuse to completely diffuse (even light image).
Delamination
Luminaires provided with a casting resin should also be monitored when it comes to heat management. This is because the housing and the casting resin have different coefficients of expansion (elongation and shrinkage). Because at high temperatures the difference becomes too great, there is a chance that the casting resin will come loose from the housing. For more information about delamination click here.
High quality light image
Smoothing the surface is essential for certain applications. This is done by means of face milling. To guarantee a high-quality light image, LuxaLight has a milling machine that can mill without affecting the light image.
Finishing
During the finishing (polishing) of the top layer of polyurethane or silicone, LuxaLight can adapt the finish to the requirements of the assignment. LuxaLight uses various finishing methods from completely matt to fully glossy (high gloss). Even a textured finish is possible. Projects that require a completely seamless finish, such as light lines in a natural stone floor, are cast and finished on location.
If you would like more information about LED moulding, please contact us, tel: 040 202 49 04.
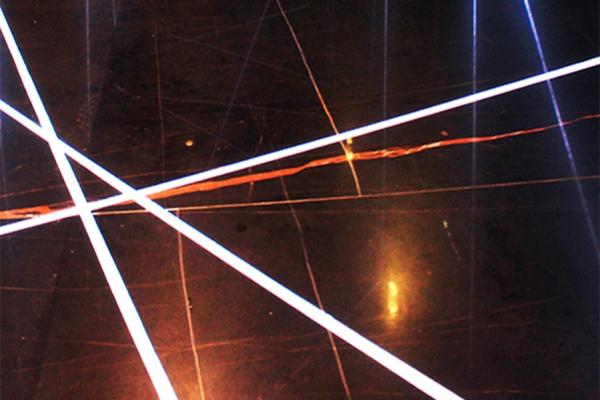
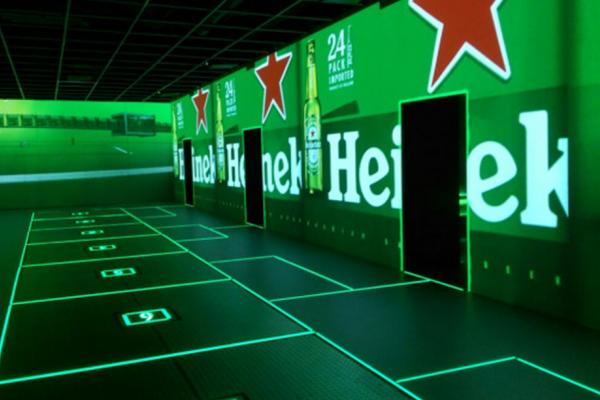
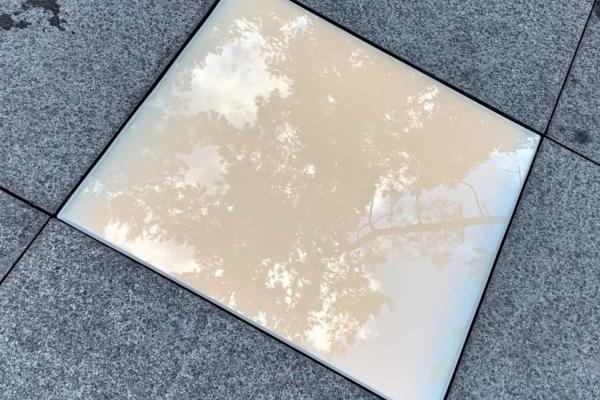
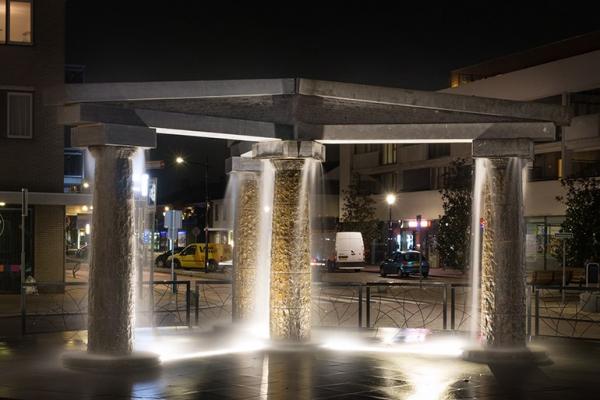